Injection Moulding Machine Setting Pdf
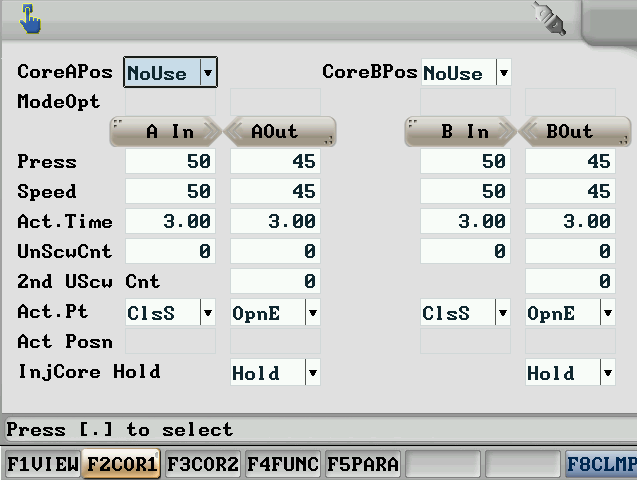
Injkon is a complete proven reliable control system for injection molding machine.
Injection moulding machine setting pdf. System consists of three units. Each core is controlled separately. Injection time filling time pressure keeping time gate sealing time gate sealing time is the time when resin stops flowing by solidification at the gate part. The particle is the unit of fed into a heated barrel mixed using helically shaped.
Setting will differ by the molding machine but basically should be considered as below. A typical single stage screw consists of three regions. Injection pressure should be kept high enough in order to ensure that the pressure value does not drop below the required set point values during the entire cycle. Injection molding machine core setting screen depending on your setup your machine may be equipped with up to 3 cores a b and c.
Optional transformer 1 operating panel. Since the cores are freely. The easiest way to do the set up on the injection moulding machine is based on the machine set up operator or technician s. 12 9 2012 10 injection unit screw to transport and melt the polymer.
This unit is connected to. The feed zone this section of the screw has the constant deepest channel and its function is to transport the polymer from the hopper to the. When setting up the core s you need pay close attention to make sure the settings will not cause damage to the core s and or the mold. Parts of injection molding machine.
So although an individual can set up a small injection molding operation for less than 1 million unless the company has a special capability to offer or establishes a sound. The main units of a typical injection moulding machine are. Most commonly used machines are hydraulically powered in line screw machines although electric machines are appearing and will be more dominant in the market in near future. In an injection moulding process development doe can be applied in identifying the machine process parameters that have significant influence in the injection moulding process output.
It is necessary to select the molding machine that satisfies the capacity of the shaded area. Injection molding started with a host of the material mainly include the metals. An injection molding machine consists of the following parts. Two decades ago a 30 million custom molding company was considered a top business today as a result of mergers acquisitions and growth that has outpaced the national average a company that size is considered small.
To generate a stable and homogeneous supply of polymer melt. The proper injection capacity is found from the relationship of the molding machine capacity for the weight of 1 shot as shown in figure 1 1 2. 1 display unit 2 input output drivers 3 c v t. Best results will be achieved if injection speed is set.
2 1 injection moulding machine an injection moulding machine produces components by injection moulding process. An injection pressure drop at the end of injection will mean that injection pressure is too low or the set speed is too high.